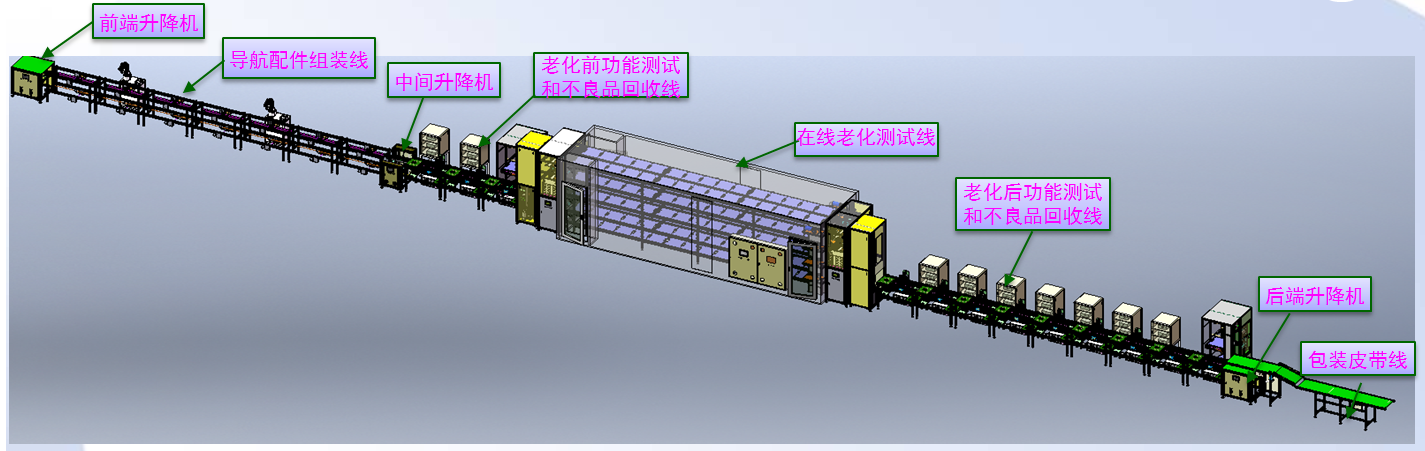
1.Product Overview:
Production of car navigation automated test line body: assembly + pre-test + online aging + post-test + finished product packaging. Intermediate aisle, transmission through the wall, integrated design, reduce logistics personnel. Vehicle Navigation Test Line
2. Equipment Features:
1. Integrated production of navigation: assembly + pre-test + online aging + post-test + finished product packaging. Intermediate aisle, transmission through the wall, integrated design, reduce logistics personnel;
2. The assembly station adopts the European standard line body carrier plate transmission, and the screw station adopts the precision positioning joint robot to drive the screws online, and uses the lower return plate to lift and turn around to reduce the floor space.
3. The whole process of test aging section is electrified, which reduces product start-up time, improves work efficiency, and shortens production tact.
4. Automatic scanning, automatic testing, and automatic recycling of defective equipment, reducing the number of operators;
3.The Main Technical Parameters
1. The equipment is a SCARA robot vision screw machine, with barcode scanning function, data upload to MES system, and use with the line body (placed next to the assembly line body).
2. Working height: 900mm±10 (Line track height);
3. Line configuration: 4-axis manipulator, 2 sets of screw feeders, intelligent electric batch, industrial barcode camera;
4. The equipment should conform to ergonomics, meet the requirements of safe production, and have a beautiful appearance. Where there are potential safety hazards, there should be corresponding safety protection facilities and devices;
5. Install 1 dual-interface electrostatic alarm/station; install three-color lights, and automatically alarm when the equipment is abnormal;
6. Torque range: 1~5.5kgf.cm, torque control accuracy: ±5%, with torque feedback and torque display function, torque feedback accuracy: ±5% (specifications can be customized);
7. Torque parameters can be designed and stored through software, which is convenient for quick replacement of models;
8. Can be connected with MES system of customer company, functions: SOP projection screen display function, component binding, overall OK/NG information of product report, actual fixed torque and OK/NG information of each screw;
9. Equipment programming: industrial computer + display;
10. The start button of the equipment is marked in green, and the emergency brake button is marked in red. And each button cannot protrude from the surface of the device by 10mm. The outer periphery of the button is equipped with an anti-mispress device, and there is a black silk screen logo next to it.
4.Equipment parameters
1. Equipment composition :
A. Front end lift
B. Navigation accessories assembly line (5 people)
Included: Seven-section 1.5-meter European standard belt assembly line, equipped with 2 multi-joint robot screw machines
C. Intermediate lift
D. Pre-aging functional test and defective product recycling line (1 person)
Include: 1. Three sections of 1.2m 2.5x speed test line
2. Two sets of test cabinets
3. A set of defective product recycling machine (can store 5 tooling boards)
E. Online aging test line
Include: 1. Two sets of four-story lifts
2. Two sets of four-layer translational conveyors
3. A set of four-story online aging room (120 seats in four-story and two-row)
F. Function test after aging and defective product recovery line (5 persons)
Include: 1. Nine sections of 1.2 meters 2.5 times speed test line
2. Seven sets of test cabinets
3. A set of defective product recycling machine (can store 5 tooling boards)
G. Rear lift
H. Packing belt line
2. Overall planning layout
Tooling size: 200*200*9.5, place 4 products